Learn the quick and easy steps to calculate the cost of goods sold (COGS) for your business.
Ever wondered where your money flees when running a business? Enter COGS, the all-revealing genie in your accounting lamp!
Calculating the cost of goods sold helps untangle the mystery of your expenses. Want to know how direct materials, labor, and overheads dance together in this financial waltz?
Stick around, because we’re unpacking the full recipe to master COGS and translate it into pricing, tax benefits, and operational zen. Ready to tame those elusive costs? Keep reading for the ultimate guide!
Key takeaways:
- COGS is the direct cost of producing goods sold
- Direct materials, labor, overheads, and inventory contribute to COGS
- Understanding COGS helps with pricing, taxes, and efficiency
- COGS includes raw materials, labor, manufacturing supplies, overheads, and shipping costs
- COGS calculation: Beginning Inventory + Additional Inventory – Ending Inventory = COGS
What Is Cost of Goods Sold (COGS)?
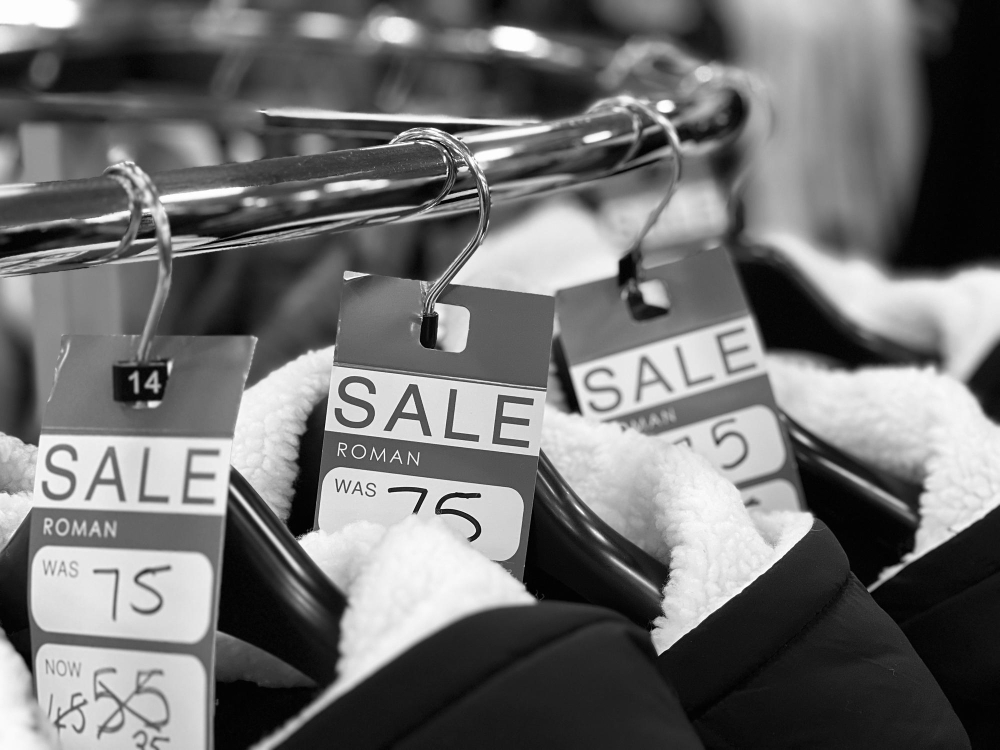
It’s the figure that shows the direct costs of producing goods that your business has sold during a specific period. Imagine it as the secret ingredient in your business recipe, revealing how much it actually costs to produce what you sell.
Several elements make up this magical number:
- Direct Materials – Think of raw materials. For a baker, it’s the flour. For a tech inventor, it’s the microchips.
- Direct Labor – This is the cost of added hands that made the product happen. Wages for your dedicated team.
- Production Overheads – The lights, the machinery, and the nice coffee machine in the corner. All those little expenses that keep production rolling.
- Inventory Beginning and Ending – It’s all about tracking. What’s in your stock at the start and what’s left at the end.
Each of these components contributes to the grand tally, showing you the true cost behind your sales. Unveiling COGS is like exposing the magician behind the curtain in your profit show.
Why Is Cost of Goods Sold (COGS) Important?
Grasping the essence of COGS is like discovering the secret level in a video game—it opens up a world of benefits. Understanding this cost helps you see how much you’re spending to create your products. Why is this handy?
First, it helps with pricing. Knowing your COGS ensures you price your products sensibly, covering costs while making a profit. Next, it’s a tax wizard. Deducting COGS from your revenue can lower your taxable income, which might mean paying less in taxes. That’s a win.
Finally, understanding COGS lets you pinpoint where you can trim the fat in your production process, thus optimizing efficiency. And who doesn’t love efficiency? So, strap in and master those numbers; your bottom line will thank you.
What Is Included in the Cost of Goods Sold (COGS)?
Think of COGS as the sum of all the direct costs linked to the production of your goods. Yes, everything and the kitchen sink (assuming it helps you make stuff).
First up, any raw materials are a no-brainer. If you’re making custom furniture, that’s your wood, nails, varnish, and tears of frustration.
Then, we have direct labor. Pay your workers, or yourself if you’ve single-handedly taken on the role of a one-person factory.
Oh, and don’t forget manufacturing supplies. Those glue sticks and sandpaper discs add up quicker than you’d think.
Factory overheads also make the cut—things like utility costs in your shop or depreciation on that whirring piece of machinery in the corner.
Finally, any inbound shipping costs to get this wonder-material to your doorstep matter too. What’s a superhero cape without its shipping label, right?
Understanding these components helps keep you in the know, like having a backstage pass to your own business concert. So, there you have it—your all-star cast of COGS ingredients!
How Do You Calculate Cost of Goods Sold (COGS)?
Alright, let’s roll up our sleeves and dive into the nitty-gritty. The process involves three main steps and a dash of basic arithmetic. Sound fun? Maybe not, but it’s essential.
First, start with your Beginning Inventory. This is the stuff you already had on January 1st or the start of your accounting period. It’s like leftovers from the previous year, but hopefully, it’s more appetizing.
Next, add in all the Additional Inventory. This heap includes everything you’ve purchased or manufactured during the period. Think of it as your shopping spree receipt but less exciting.
Finally, subtract your Ending Inventory. Basically, what’s left on December 31st or whenever your accounting period wraps up. Remember, what’s sitting in your storeroom doesn’t count as sold. It’s like those socks in your drawer you swear you’ll wear one day.
Here’s the magic formula: Beginning Inventory + Additional Inventory – Ending Inventory = COGS. Voila! You’ve cracked the code.
Wondering if you can slip in the cost of your daily espresso in this? Nice try. Stick to the cost of raw materials, labor directly tied to production, and those pesky factory overheads. Simple enough? Now go forth and calculate like a pro!
Beginning Inventory
Imagine your business is starting the year with a treasure trove of goods ready to sell. That stash is your loyal Beginning Inventory. It’s the backbone from last period, rolling over to give you a head start.
First thing you do: Check the shelves and count, count, count. Ensure everything from widgets to whatchamacallits is accounted for.
Once you’ve got the numbers, attach a price tag. What did you pay for these golden nuggets? This includes direct costs like raw materials but holds off on rent or utilities. We’re keeping it strict and simple.
Don’t overlook that sneaky little gremlin called shrinkage. Lost a few items to damage or mischief? Note it down! Accuracy is key.
Bit by bit, your Beginning Inventory stands as the gatekeeper to figuring out just how much you really sold and made this glorious financial cycle.
Additional Inventory
Ah, additional inventory, the hidden treasure waiting to be discovered in the cost of goods sold calculation!
This is all about purchases and acquisitions. Think of it as stocking up your pantry. Everything you buy to make your goods – raw materials, components, that fancy new gadget that slices tomatoes at lightning speed – counts here.
Here are some examples:
- Supplies and materials bought during the period
- Shipping costs tied to these new purchases
- Direct labor, if it’s directly associated with making products
Imagine a soapmaker splurging on lavender essential oil, coconut oil, and those jazzy little molds. That’s all part of the additional inventory. So get those receipts ready and add up those costs!
Ending Inventory
Ending inventory is the value of the goods remaining at the end of an accounting period. It’s crucial for pinpointing your COGS and understanding the health of your business. Here’s what you need to know:
First, take a physical count of your inventory. Yes, it’s tedious, but it’s essential unless you have a magical inventory-vanishing wand.
Second, value your inventory. Use either the First-In, First-Out (FIFO) method or the Last-In, First-Out (LIFO) method. Just promise not to do eeny-meeny-miny-mo with it.
Lastly, consider any damaged or unsellable goods. These should be valued based on what you can actually get for them, not what you wish you could. Bye-bye, broken widgets.
Nailing these steps ensures you accurately calculate your ending inventory, which in turn keeps your COGS numbers honest. Plus, it keeps your accountant from giving you the side-eye at tax time.
COGS Example A: The Woodworker
Imagine you’re a woodworker extraordinaire. You’ve got a workshop filled with sawdust, creativity, and dreams of wooden marvels. You start the year with $5,000 worth of lumber, nails, and other materials – that’s your beginning inventory. Throughout the year, you buy more materials for $15,000 because special wooden treasures don’t build themselves.
At the end of the year, after crafting tables, chairs, and maybe an overly enthusiastic sculpture of a duck, you find you still have $3,000 worth of materials left. Here’s the math:
- Start with your beginning inventory: $5,000
- Add in your additional purchases: $15,000
- Subtract your ending inventory: $3,000
Your Cost of Goods Sold (COGS) for the year? It’s $17,000. That’s the cost of the materials you transformed from humble planks to majestic furniture. Voilà! COGS decoded.
COGS Example B: The Soapmaker
Meet Sally, a soapmaker extraordinaire. Sally’s shelves overflow with handcrafted, fragrant bars of sudsy goodness. To calculate her COGS, she completes a simple equation.
First, Sally notes her beginning inventory on January 1: 200 bars of soap valued at $400.
Next, she adds additional inventory costs over the year. She spends $600 on raw materials like essential oils, shea butter, and natural dyes. Plus, she lays out another $200 for production supplies.
Now, Sally checks her ending inventory on December 31: 100 bars of soap worth $200.
With these numbers, Sally’s COGS looks like this:
- Beginning inventory: $400
- + Additional inventory: $800 ($600 raw materials + $200 production supplies)
- Ending inventory: $200
Her COGS totals $1,000.
Voilà! Sally’s ready to wash her hands and crunch more numbers.